The Facts About Alcast Company Uncovered
Alcast Company Can Be Fun For Everyone
Table of ContentsSome Ideas on Alcast Company You Need To KnowUnknown Facts About Alcast CompanyFascination About Alcast CompanyAlcast Company - QuestionsFascination About Alcast CompanyAlcast Company Fundamentals Explained
Chemical Comparison of Cast Aluminum Alloys Silicon advertises castability by reducing the alloy's melting temperature and improving fluidity throughout spreading. In addition, silicon adds to the alloy's toughness and wear resistance, making it important in applications where longevity is crucial, such as automobile components and engine elements.It likewise improves the machinability of the alloy, making it less complicated to refine right into finished items. In this means, iron contributes to the general workability of aluminum alloys.
Manganese contributes to the toughness of aluminum alloys and improves workability (Casting Foundry). It is commonly utilized in wrought light weight aluminum products like sheets, extrusions, and profiles. The existence of manganese aids in the alloy's formability and resistance to splitting during construction procedures. Magnesium is a lightweight component that gives stamina and influence resistance to light weight aluminum alloys.
Some Ideas on Alcast Company You Should Know
Zinc boosts the castability of aluminum alloys and helps control the solidification process throughout spreading. It boosts the alloy's stamina and solidity.

The key thermal conductivity, tensile stamina, return stamina, and elongation differ. Among the above alloys, A356 has the highest possible thermal conductivity, and A380 and ADC12 have the most affordable.
Alcast Company Fundamentals Explained
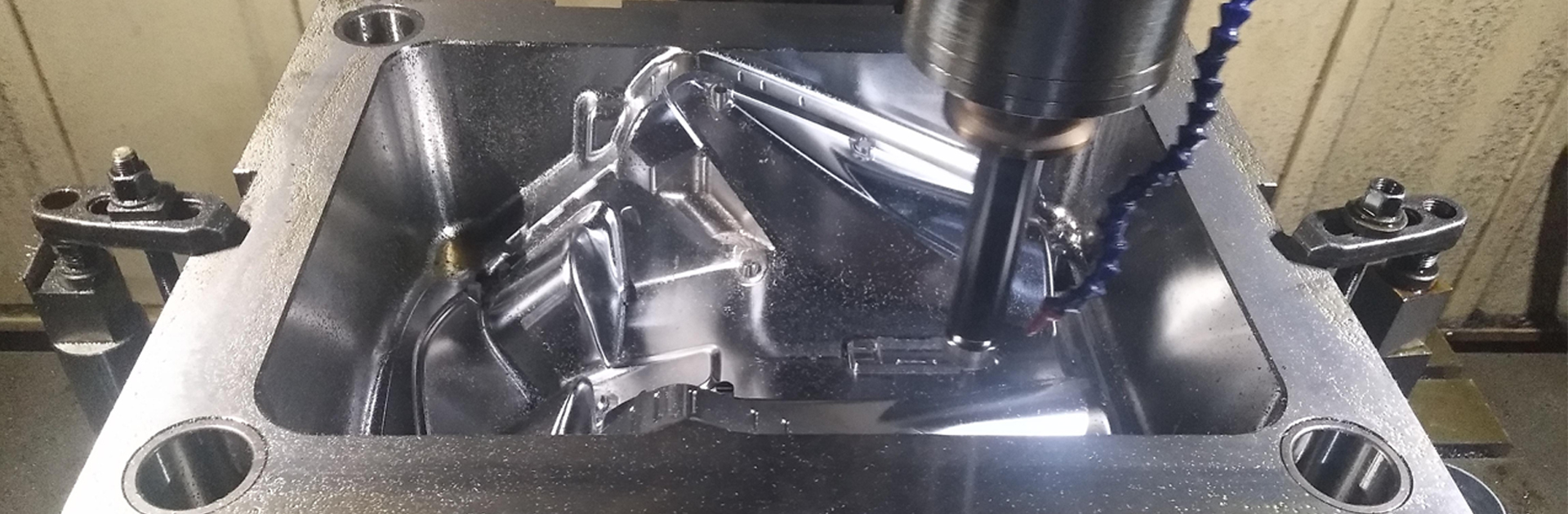
In precision spreading, 6063 is well-suited for applications where complex geometries and this premium surface area finishes are vital. Examples include telecommunication units, where the alloy's exceptional formability permits sleek and visually pleasing styles while keeping structural stability. In the Illumination Solutions industry, precision-cast 6063 components develop sophisticated and reliable lights fixtures that require elaborate forms and good thermal performance.
The A360 exhibits exceptional elongation, making it ideal for complex and thin-walled components. In accuracy spreading applications, A360 is appropriate for markets such as Consumer Electronics, Telecommunication, and Power Tools.
Alcast Company Things To Know Before You Get This
Its special properties make A360 a useful choice for precision spreading in these markets, improving item resilience and top quality. Casting Foundry. Aluminum alloy 380, or A380, is a widely used casting alloy with several distinctive qualities.
In accuracy casting, light weight aluminum 413 radiates in the Consumer Electronic Devices and Power Equipment industries. This alloy's premium rust resistance makes it an exceptional option for outdoor applications, guaranteeing lasting, long lasting items in the pointed out sectors.
Getting My Alcast Company To Work
The aluminum alloy you choose will significantly impact both the spreading procedure and the residential properties of the last item. Because of this, you should make your decision very carefully and take an informed method.
Identifying the most ideal light weight aluminum alloy for your application will imply weighing a vast selection of features. The very first classification addresses alloy attributes that influence the production procedure.
The Main Principles Of Alcast Company
The alloy you choose for die casting straight affects several elements of the casting process, like how easy the alloy is to collaborate with and if it is vulnerable to casting issues. Warm breaking, also referred to as solidification cracking, is a common die spreading defect for light weight aluminum alloys that can result in interior or surface-level rips or cracks.
Particular aluminum alloys are a lot more at risk to hot fracturing than others, and your selection must consider this. One more common defect located in the die spreading of aluminum is pass away soldering, which is when the actors sticks to the die wall surfaces and makes ejection challenging. It can harm both the actors and the die, so you ought to try to find alloys with high anti-soldering properties.
Rust resistance, which is currently a notable feature of aluminum, can differ significantly from alloy to alloy and is a vital particular to take into consideration depending on the environmental conditions your product will be subjected to (Aluminum Castings). Wear resistance is an additional property generally sought in light weight aluminum items and can set apart some alloys